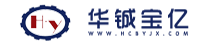
1 前言
1.1 目前污水厂污泥处理的现状形势
污水类型是以冶炼、石油化工为主的工业污水,废水中含有油类、氰化物、酚类、硫、砷、芳烃、酮类等污染物质,毒性较强、成分复杂。根据环保局的要求,工业污水处理厂产生的污泥暂定为危险废物,因此,亟需新建工程处理污泥,防止对环境造成二次污染。
目前,产生的污泥是外送至其他危废处置厂处置,处理成本极高,而且污泥量远超过危废处置厂的处理能力。成本高和处置量极不平衡的矛盾日益突出。
1.2 污泥处理处置工程的必要性
污水厂污泥处理处置工程主要处理的是规模为3万m³/d工业污水处理后所产生的污泥,同时接纳开发区内工业企业所产生的危废污泥。
首先,项目是为解决自身工业污水处理产生的危废污泥找出路,保障该园区内的工业污水处理能力,是环境保护的需要。其次,该园区内一大批工业项目即将建成,其配套的污水处理和污泥处理设施也同步建成。该项目的投产解决了污泥的出路,保证了其他招商引资项目的顺利进行,是经济发展的迫切需要。再者,干化后的污泥其热值较高,有效地减少了辅助燃料的投入,能大幅度降低能耗,污泥焚烧后仅剩10%的无机灰分,能做到较大限度的减量化,是节能减排的需要。
因此,为彻底解决工业污水处理和该园区内工业污水处理站产生的危废污泥,尽快筹建污泥处理处置工程十分必要。
1.3 污泥处理处置工艺的技术特点和优势
工程的污泥处理处置技术采用的是干化焚烧方案,主要由三个单元构成,即薄层干化单元、焚烧单元、余热利用烟气处理单元。
脱水污泥的含水率为80%,其热值不足以维持干化焚烧工艺的正常运行,存在能量缺口,必须添加热源。项目地处石化园区,项目建设地点能因地制宜地选择和利用清洁能源,确保稳定运行,达到经济可靠的需求,这是项目工程技术定位的关键因素和主要优势。
薄层干化单元在国内危废污泥处理处置行业有成熟的业绩。其系统简单,工艺成熟,既可以半干化,又可以全干化,两者可以灵活调节,对污泥泥质的波动技术适应性较强;设备数量少,占地面积较小;系统单元为低氧运行,杜绝粉尘爆炸的危险性,具备较高的安全性。
焚烧单元采用回转窑焚烧炉和二燃室组合,回转窑炉可处理多种废物,对废物的适应性较广。污泥在焚烧时间固相停留时间>1h,不会出现“短流”现象,气相停留时间易于控制,再通过后设二燃室保证废物的完全焚烧,在高温运行条件下操作的稳定性较好。
烟气净化采用“SNCR+急冷半干式喷淋+袋式除尘+SCR+湿式洗涤+烟气再热”的高标准组合工艺,有害物质去除率较高,反应剂消耗量较少,可以有效控制二恶英。
2 工程简介
2.1 污泥处理处置工程的建设内容
建设内容包括污泥干化、污泥焚烧、烟气处理、配套设施。
2.2 工程建设规模论证分析
工程拟分两期建设,总处理规模为24tDS/d,目前一期工程建设规模确定为12tDS/d。
3 工程处理处置污泥的特性分析
3.1 处理处置对象
工程处理处置对象主要针对目前一期工业污水处理所产生的危废污泥,同时兼顾该石化经济技术开发区内各工业企业污水处理厂产生的危废污泥。
3.2 危废污泥主要来源
以炼油、石油化工为主的工业污水,废水中含有油类、氰化物、酚类、硫、砷、芳烃、酮类等高污染物质,COD较高,毒性较强,成分复杂。根据 和当地的相关文件,此类污水处理后所产生的污泥需作为危险废物进行处理与处置。
3.3 泥质特点
工业污水处理厂产生的脱水后污泥含水率一般在78%~82%,其性质为软性固体、糊状、褐色、异臭味较浓、伴有氨气、硫醚臭等刺激性气味,比重约为1.1t/m³。
3.4 污泥组分
污泥中有机成分复杂,含有大量的蛋白质、氨基酸、脂肪、维生素、矿物油、洗涤剂、腐殖质、细菌及代谢物、各种含氮、含硫物质、挥发性异臭物、致病微生物等。
污泥中的无机成分有矿物盐(硝酸盐、亚硝酸盐、氨盐等)、石灰类(干CaO或含水的Ca(OH)2等)、砂类(SiO2)和灰分。
结合现有工业污水处理单元所产生的污泥分类,其中物化处理单元的污泥热值为8.41MJ/kg(折合约2009kcal/kg);生化处理单元的污泥为12.35MJ/kg(折合约2950kcal/kg)。根据工程可行性研究报告的论证分析结论,污泥的干燥基热值按照2680kcal/kg设计。
4 污泥处理处置工程确定的技术标准
4.1 污泥干化处理指标
污泥干化处理指标如下表所示:
污泥类别 | 含水率 | 暂定含水率标准 |
脱水污泥 | 75%~85% | 80% |
半干污泥 | 30%~40% | 35% |
全干污泥 | 10%~20% | 10% |
污水处理厂污泥脱水后含水率一般在75%~85%,其性质为软性固体,褐色,异臭味浓,比重约为1.01t/m³。为使后续污泥干化焚烧设施能够经济高效运行,污水处理单元中污泥脱水设施原则上应满足标准《城镇污水处理厂污泥泥质》(GB 24188-2009)中规定的含水率小于80%的要求。但为确保系统对脱水污泥的受纳缓冲能力,充分考虑了污泥含水率的波动对系统处理能力的影响。
4.2 污泥焚烧技术指标
污泥焚烧技术指标如下表所示:
受控项目 | 焚烧炉温/℃ | 烟气停留时间/s | 焚烧效率 | 焚毁去除率 | 残渣热灼减率 |
处理指标 | ≥1100 | ≥2.0 | ≥99.9% | 99.99% | <5% |
对于常规的污泥干化焚烧系统,炉膛出口温度需达到850℃,但该工程是危险废物焚烧,燃烧温度按照≥1100℃是强制性规定。
4.3 烟气处理技术指标
污泥焚烧过程中产生的烟气控制目标执行环评批复要求的烟气排放标准,即《危险废物焚烧污染控制标准》(GB 18484-2001)中大气污染物排放限制(二恶英执行0.1 TEQ ng/m³)和《大气污染物综合排放标准》(GB 16297-1996)中二级标准,通过45m的高烟囱排放。
4.4 臭气处理后的技术指标
臭气处理后需满足《恶臭污染物排放标准》(GB 14554-1993)中的二级标准。
4.5 废水处理指标
系统产生的所有废水经本厂内管网收集后排入工业污水处理厂。
5 工程整体处置工艺应用分析
5.1 污泥处理处置整体工艺
根据《污水厂污泥处理处置工程可行性研究报告》评审结论,工程污泥处理处置推荐采用污泥干化+污泥焚烧工艺。
5.1.1 污泥干化工艺分析
工程的污泥属于危险废物,工艺设计端主要以下面四个方面作为干化设备选型的原则。
(1)在国内污水厂污泥处理和危废污泥处理处置行业内拥有良好的使用业绩,需具有两个以上的工程应用实例,其中至少有1个工程已稳定运行1年以上,至少有1个工程属于危废污泥处理处置业绩。
(2)系统简单,工艺成熟,对污泥泥质波动的适应性强。
(3)污泥的干化系统应该具有较高的安全性。
(4)干化厂恶臭污染物和噪声的控制与防治应符合 相关标准的规定。
适合污泥干化类型有流化床式、圆盘式、两段式、薄层式、桨叶式5种。
相对来说,薄层干化机工艺简洁成熟、安全性高、经济适应性好,且在国内有化工危废污泥的干化业绩。因此,经过论证分析,选择薄层污泥干化工艺。
5.1.2 污泥焚烧工艺分析
适合工程的焚烧炉型有机械炉排、回转窑、流化床焚烧炉三种。根据项目的特点,选择回转窑焚烧炉更为合适。
回转窑焚烧炉对焚烧废物的适应性强,技术成熟,运行可靠,简单,可很好地满足各种危废焚烧的进料、出渣、燃烧完全等方面的要求。因此,原则回转窑焚烧工艺,采用顺流布置。
5.2 脱水污泥接收系统
工艺配置:汽车衡+湿污泥接收仓+双螺旋喂料机+单螺杆输送泵。
车载或袋装含水率为80%的湿污泥经汽车衡称重计量后倒入地下室湿污泥接收仓,经脱水污泥输送泵输送至污泥干化车间的污泥干燥机内,这个过程实现了污泥的进料。
主要设备技术参数:汽车衡1套,80t量程;湿污泥接收仓1套,容积为30m³;单螺杆输送泵2套,输送能力为3m³/h,H=100m,11kW,一用一备。
5.3 污泥干化系统
工艺配置:薄层干化器+线性干化器+产品冷却器。
薄层干化处理线2条(1用1备),单线平均污泥处理量为60t/d(含水率80%计),出泥为半干污泥,含水率为35%;单台薄层干化器的蒸发面积为50㎡。蒸汽进口参数:温度为180℃,压力为1.0MPa,单台干燥机的理论耗气量为2330kg/h。
含水率为80%的脱水污泥由污泥泵送入薄层干化器,在蒸汽的加热下,含水率由80%降为35%左右,实现了污泥的半干化,之后送至回转窑焚烧炉焚烧处置。
线性干化处理线1条,处理量为769kg/h,污泥进口含水率为35%,出泥含水率为10%,蒸发面积为50㎡。蒸汽进口参数:温度为180℃,压力为1.0MPa,理论耗气量为253kg/h。
当污泥焚烧出现故障检修或者例行检修时,启动线性干化机,将污泥含水率降至10%。这个过程就是将薄层干化机出口的含水率为35%的半干污泥通过螺旋输送机输送至线性干化机器,通过调整热媒流量和温度实现污泥的含水率达到10%,进行理论全干污泥的生产调节。
产品冷却器处理线1条,处理能力为1.8t/h,污泥进口温度为110℃,出口温度为≤45℃,自薄层干化器或启动的线性干化机生产的半干污泥产品进入污泥冷却器。冷却器是一种带有夹套的螺旋,外壳与轴都通冷却水,污泥产品被壳体、转轴内流动的冷却水冷却,冷却后的产品污泥可以直接装车外运,也可以输送至干化产品料仓内暂存,等待后续处理和应用。
5.4 干污泥输送及存储系统
工艺配置:双向链板、斗式提升机、双向螺旋、料仓存储。
半干污泥含水率为35%,全干污泥含水率为10%;干污泥湿度<45℃;全干污泥料仓数量2座,有效容积为30m³;外来污泥接收仓1座,有效容积为21m³。
干污泥输送机存储系统设置的目的有两个:一是为了实现干化后的污泥直接进入回转窑进料机构进行焚烧处置;二是当污泥焚烧炉进行故障或理性检修时,干污泥通过倾斜螺旋底部的分料器进入双向链板输送机,斗式提升机将干污泥再提升至双向螺旋分别分配给室外两个暂存料仓,并能实现装车外运。
当焚烧检修完毕恢复正常后,暂存料仓再通过双向链板的反转,再将污泥送入焚烧系统进行处理。
5.5 污泥焚烧系统分析
在焚烧系统集成方面,首先要定位和遵守的原则有以下几个方面:
(1)污泥焚烧将遵循“减量化、无害化、稳定化、资源化”的方针。
(2)以成熟成套危废处理技术、工艺为基础,进行针对性的专门设计。
(3)选用设备成熟可靠,强化关键设备的耐腐蚀、抗高温氧化处理和低故障、长期连续稳定运行性能。
(4)操作的高效性和灵活性。
(5)确保满足焚烧炉、烟气排放、环境噪声等环保指标。
(6)较大限度的余热利用。
(7)尽可能低的运行、维修、养护费用。
工艺配置:回转窑焚烧炉+二燃室焚烧。
焚烧系统处理线1条,焚烧系统进泥含水率为35%,焚烧处理能力为18.5t/d(含水率35%的污泥)。
5.5.1 回转窑技术参数确定及性能特点分析
筒体尺寸为Φ2.4×8m,转速为0.12~1.2r/min,窑体倾斜度为0.03,采用顺流式布置,燃烧温度为800~1000℃。
工程设计选择的回转窑焚烧炉充分具备如下特点:
(1)污泥焚烧时翻腾前进,热力学的三种传热方式并存,热利用率高。
(2)高温物料接触耐火材料,更换炉衬方便,维护检修成本低。
(3)传动机理简单,传动机构在筒体外壳,设备维修简单。
(4)对焚烧物的形状、含水率要求不高。
(5)良好的密封措施和炉膛负压,保证有害气体不外泄。
5.5.2 二燃室焚烧技术参数及性能特点分析
二燃室外径尺寸为Φ3.2×13.4m,筒体壁厚为10mm。保温材料配置情况:外表面温度为60℃,耐热层§180,保温层§180,绝热层§90。二燃室烟气出口温度为1100~1200℃,烟气滞留时间>2s,二燃室设有检修门、并设温度、压力、氧量仪表等安全附件。
该二燃室的技术特征分析如下:
(1)在二燃室顶部设有紧急排放烟囱,保证在发生紧急停炉条件时,高温烟气紧急导排导大气中。
(2)整体采用钢制圆形结构,不存在烟气死角,空间利用率高。
(3)在结构设计上严格执行了高停留时间>2s,烟气焚烧温度>1100℃,烟气与燃气的高湍流混合度。
(4)二燃室内配置了二次风设计,多点切向强制供风,确保焚烧分解彻底。
(5)完善的监测控制技术设计,安装有压力、温度、氧量仪等,能在线监测污泥的焚烧工况。
(6)独特的防结灰设计,立式结构,便于烟气流速控制,本质上具有自清灰能力。
(7)设有安全保护装置,防止炉内爆炸,一旦在停水、停电紧急状态时,紧急排放烟囱打开,将炉内的高温烟气安全地排放到大气中去,该装置安装在二燃室顶部2.5m高空位置,其技术参数为φ1.0×2.5m,内径为0.6m,采用浇注料保温,与二燃室采用法兰连接,防爆开盖采用气动形式,立式安装。
5.6 余热利用系统
工艺设备:采用余热锅炉回收热量。
膜式水冷壁锅炉1台,锅炉给水温度为104℃,蒸发量为1.9t/h,蒸发波动为1.5~2.0t/h。蒸汽参数:184℃,1.1MPa,运行压力为1.1MPa。锅炉进口的高温烟气温度为1100℃,出口温度为550℃。蒸汽汽包为4m³,¢1.0×5.5m。锅炉结构为双回程膜式水冷壁结构,其锅炉本体的附属配件有卸灰螺旋、1个电动叶片卸灰阀、2个SNCR喷嘴等。
余热利用系统设计主要是利用烟气中的余热产生蒸汽,高温烟气的热量在余热锅炉内被回收,烟气温度由1100℃降至550℃,产生的蒸汽用于污泥的干燥单元。干燥污泥后的蒸汽被冷凝成冷凝水再回到余热锅炉循环利用,达到经济运行的目的。
5.7 烟气处理系统技术设计分析
工艺路线:SNCR+急冷半干式脱酸塔+袋式除尘器+SCR+湿式洗涤+GGH。
烟气净化处理线1条,烟气处理量为4237Nm³/h(按余热锅炉出口烟气量计)。根据污泥中所含污染物的成分分析,其焚烧后烟气中的污染物大致分为以下几种:
(1)不完全燃烧物:碳氢化合物燃烧后产生的无害的二氧化碳和水,可以直排。在燃烧不良时产生一氧化碳、炭黑、烃、烯、酮、醇、有机酸和聚合物。
(2)粉尘:包括污泥中的惰性金属盐,通过袋式除尘器、湿法洗涤法去除。
(3)酸性气体:氯化物、卤化氢、硫化物、氮氧化物、无氧化磷等,通过急冷半干式脱酸塔、湿式洗涤法去除。
(4)重金属物:铅、汞、铬、镉、砷等的元素态、氧化物及氯化物等。其中可挥发的金属物在低温去自行凝结颗粒被飞灰吸附后,通过袋式除尘器截滤下来;部分不凝性不易吸附的金属氯化物,利用其溶于水的特性在湿法洗涤塔内去除。
(5)二恶英类:本项目采取的技术措施有三种。 是在回转窑焚烧阶段保持>800℃的高温工况,抑制其合成量;第二是烟气管路中喷入活性炭吸附二恶英生成的前驱物HCl,及其合成反应的催化剂重金属等;第三是保证急冷半干脱酸塔的入口温度在500℃左右,出口温度在200℃以下,冷却时间<1s,有效避开二恶英的再合成。
(6)NOx:采用两级脱氮工艺,在余热锅炉处设置了SNCR法,控制NOx,第二级在袋式除尘器之后甚至SCR法反应器,进一步控制了NOx。
5.8 公共辅助系统
公共辅助系统主要用于辅助污泥干化焚烧及烟气处理系统的运行,包括碱液制备、化水制备、液氨车间、灰渣收集、压缩空气、CEMS系统等。
6 工程设计投资、建造、后期运营情况分析
6.1 工程投资分析依据
按照当地现行的建筑工程概算定额,当地现行的建设工程建安工程费用计算程序表,当地现行的市政工程设计概算编制办法,当地当时的建设工程造价信息季度信息表,结合同领域类似工程技术经济指标,工程总投资为21190.45万元,其中干化焚烧工程直接费用为13786.99万元,设计单位处理成本为1372.10元/t(含水率按80%计),单位经营成本为749.10元/t(含水率按80%计)。
6.2 工程投资回收期分析
项目资金来源70%为银行贷款(贷款利率按6.55%计),30%为自筹资金,建设期一年左右。
污水厂污泥处理处置收费标准按980元/t计算,项目投资财务内部收益率为9.09%(税前),大于行业基准收益率5%,项目投资回收期为10.15年(税前),小于行业基准投资回收期18年。
7 工程效益和环境效益分析
7.1 投运后危废污泥处置评估
污水厂污泥处理处置工程投运后,为3万t/d工业污水处理单元运行过程中产生的脱水后危废污泥能得到有效处置提供可靠保障。经环评核定,项目的运管严格与配套建设目标一致,污泥干化焚烧处理量达到12tDS/d,折合脱水污泥60t/d(按含水率80%计),年处理污泥量≥4380tDS/a。
7.2 工程投运后的环境效益分析
投入运营后以服务社会和该石化园区为主要目的,不仅为开发区工业污水处理厂产生的污泥和各园区各工业污水处理厂产生的污泥彻底解决找到了出路,也为污水处理厂污泥处置的安全性和多样性作出新的贡献,同时也为减少污泥处理的二次污染体现出难以用货币衡量的环境效益。
工程的正式投运意味着工业污水处理厂的污泥真正朝着稳定化、无害化、减量化的方向发展,为该城市及石化经济技术开发区经济实现可持续发展作出更大的贡献。
工程建成投入商业运营管理后,开发公司将本着“保本微利”商业运作原则,向用户收取适当的危废污泥处置费,维持自身的正常运转,为更好地改善石化园区投资环境提供积极又巨大的间接经济效益。
8 结语与讨论
当前污水厂在处理污水过程中污泥量与污泥处理处置成本高是一个普遍存在的难题,且极不平衡,因此新建污泥处理处置工程,迫在眉睫且非常必要。
工程设计中的干化工艺、焚烧工艺、烟气净化工艺的路线选择和设备配置形式与其他工程案例相比已属于高标准的工艺组合。
考虑到今后污泥泥质有一定的不确定性,可能会在工程调试器针当时的泥质情况,对工艺环节进行一定的技术优化,也会导致设备的投资增加或运行成本的浮动等。