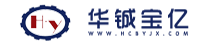
老化油又被称为油田絮凝物、油水中间过渡层、油水中间乳化层等,是原油生产、处理过程中,在药剂、机械杂质、胶质沥青质、细菌、空气、循环剪切等因素的作用下形成的。老化油在形成过程由于化学反应、固体颗粒杂质、高分子化合物、污水处理药剂及增产增注化学剂等乳化剂的混入,使其界面活性物质增加,并随时间的延长在油水界面不断富集,使界面膜的强度和厚度增加形成稳定性很高的原油乳状液,对油水分离造成较大影响。
老化油来源主要为二次、三次采油形成的乳化液颗粒;钻井作业及原油输送过程中形成的乳化液;污水处理回收的污油;回收的落地油;细菌作用下产生的含油悬浮物等。
近年来随着XM油田开发进入中后期,站外酸化压裂、调剖调驱等增油措施逐渐增多,油井采出液组成越来越复杂,导致XM油田联合站一直被老化油的问题所困扰,直接影响联合站脱水系统的稳定性,造成外输原油经常含水超标。常规热化学沉降脱水和热化学电场处理老化油效果较差,因此,急需寻找新技术和新处理工艺解决老化油问题,以提高脱水系统稳定性,提高原油商品率。
1 XM油田联合站老化油现状
XM油田联合站外输原油35万t/a,各储罐外排老化油约为8000t/a。为了减少老化油对脱水主系统的影响,2010年XM油田联合站通过流程改造,实现各储罐内老化油定期收集、单独处理。联合站老化油处理主流程为:定期将各储罐中间层老化油定期泵抽到1000m³老化油沉降罐,通过循环加药、提压、加热循环等操作流程,储罐内老化油经长时间高温热化学沉降后,储罐顶部原油含水达标后去外输系统直接外输,罐底污水去污水处理系统进一步处理。
但是,由于老化油处理采用常规热化学沉降脱水工艺流程,储罐内老化油循环加药至70℃,加药浓度达到200mg/L,沉降超过72h后,沉降罐高液位出口原油含水率仍为10%以上,远远高于0.5%,满足不了直接外输要求,影响站内正常生产。
2 室内化验结果分析
经过现场取样和室内化验分析,XM油田联合站1000m³油罐老化油是含有大量固体物质的油水强乳化液,其中,固体含量约为20%,水含量约为35%,原油含量约45%。老化油20℃时密度为0.932g/cm³,主系统净化油20℃时密度为0.868g/cm³;老化油50℃时黏度为400mPa·s,主系统净化油50℃时黏度为45mPa·s,老化油与主系统外输净化油物性差别大。老化油密度大、黏度高,导致原油流动性差,油水分离困难。
老化油组分分析结果:沥青质含量为5.89%,胶质含量为17.28%,蜡含量为69.98%,芳香化合物含量为4.78%,机械杂质含量为1.13%。组分中蜡、胶质和沥青质含量较高,而芳香化合物含量低,说明老化油中重质组分较多,轻烃类组分较少。
老化油固相分析结果:两种老化油固体杂质成分主要分为3类:一是,混入的砂土成分,包括石英、黏土等;二是,可能的结垢产物CaCO3;三是,腐蚀产生的铁和硫的化合物。具体分析结果如下表所示:
固相组分 | 含量(%) | 固相组分 | 含量(%) |
石英(α-SiO2) | 18 | 硫复铁矿(Fe3S4) | 8 |
斜长石(NaAlSi3O8) | 10 | 石盐(NaCl) | 9 |
方解石(CaCO3) | 16 | 黏土 | 30 |
黄铁矿(FeS2) | 9 |
从上表可以看出老化油中铁和硫的化合物(FeS2和Fe3S4)含量为17%,老化油中铁和硫的化合物粒径分布为3.86~50.46μm,呈胶体状态,因而,其活性较强。铁和硫的化合物作为界面活性物质,有助于油水乳化,促进油-水中间过渡层生成。
老化油水相分析结果:关键指标Fe2+,净化油水相Fe2+含量仅为36mg/L,而老化油水相Fe2+含量高达179~195mg/L;净化油水相中S2-含量仅为26mg/L,而老化油水相S2-含量高达161~202mg/L。老化油中含有较多的Fe2+、S2-,可见这两种离子对老化油的形成作用较大,初步判断FeS为老化油形成的主要原因。
根据老化油、密度、黏度、组成分析、固相分析和水相分析结果,可以判定XM老化油物性差、组分中重质组分多、固相中铁和硫的化合物含量高,水相中Fe2+和S2-含量高,这些综合因素导致XM老化油处理困难。
3 老化油室内离心分离试验
实验中使用浓度为2g/100mL的高锰酸钾溶液作为FeS去除剂,取15mL离心管,加入13mL同种老化油和0.5mL的高锰酸钾溶液。离心油样测定含水率为21%,升温至65℃后,选定不同的离心机转速和离心时间进行离心脱水对比实验,测定离心后各层体积。
从老化油离心8min后两层的含水率数据可以看出,离心力越大,油层的含水率越低,离心力1000g时,油层的含水率已低于0.5%,达到了合格原油的标准;离心力1500g时,油层中已检测不出含水。油水过渡层的含水率随离心力的增大同样呈现先增大后减小的趋势,1000g时为极值。
室内离心分离试验初步证明XM老化油离心分离具有可行性,合理的离心参数为离心力1000g、时间8min。
4 离心分离装置的构成
该离心分离装置主要由卧螺式离心分离系统、碟片式离心分离系统和加药系统3部分组成:老化油首先进入卧螺式离心分离机,在絮凝剂的作用下,实现固、液分离,分离出来的含水油进入碟片式离心机,在破乳剂的作用下实现进一步脱水。
5 现场试验情况
5.1 装置现场安装情况
老化油处理橇装设备处理量为150t/d,装置于2013年11月10日运至XM联合站现场,装置位置距离原油储罐、泵房值班室等构筑物均满足安全防火技术规范要求,经过现场组装连接并调试,于2014年1月15日具备现场试验开工条件。装置来油为联合站站内1000m³老化油储罐,装置出口合格原油去站内外输油泵出口,装置出口污水去站内污水处理系统,装置残渣出口直接用防渗密封袋打包。
5.2 现场试验情况
正式现场试验于2014年2月20日开始,至3月5日结束,试验过程中每天现场跟踪运行情况,监测节点指标变化,发现异常及时提醒现场施工人员进行调整。试验期间进装置老化油温度为45℃,含水率约为35%,装置平稳运行时加药浓度为100mg/L,装置加热炉出口温度为65℃。
5.3 现场运行效果
现场试验历经14天,合计处理老化油量1000m³,试验过程中装置运行平稳、无漏油、触电等安全事故,装置出口原油含水率,污水油含量,废渣含水,废渣油含量各项指标均达到预期要求。
5.4 运行费用
试验过程中共处理老化油1000m³(折合930t),消耗天然气2500m³,消耗电能5500kW·h,消耗破乳剂100kg,天然气价格按2.36元/m³,电价为0.55元/kW·h,破乳剂价格为2.0元/kg计算,若不含人工费,老化油离心分离综合运行费用为9.8元/t,运行费用较低。
6 结语
老化油离心脱水技术在油田联合站现场应用可行,装置实现连续平稳运行,处理后原油含水、污水油含量、污泥含水率及废渣含水率均能满足生产需求。老化油离心分离技术提高了原油商品率,处理后的废渣作为建筑空心砖原料,提高了原料利用率,有利于环境保护。采用离心分离处理后的老化油可直接外输,提高了原油商品率,经济效益良好,具有广阔的应用前景。