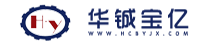
1 循环水污泥系统概况
中国铝业山东分公司循环水系统主要承担着氧化铝厂(烧结法)、化学品氧化铝公司等生产单位各工序排水的沉淀处理、冷却降温和循环供应任务。
循环水污水处理系统主要包括水处理西站、水处理东站、大泵房(蒸发循环水)三个子系统,处理工艺为传统污水处理方法。因各生产岗位排水复杂,回水水质和水量时常变化,其中水处理西站日处理污水量为2.5万m³~3万m³,水处理东站日处理污水量为2.5万m³~3万m³,大泵房系统日处理蒸发循环水量为16万m³~20万m³。
循环水污泥处理系统包括重力浓缩处理及机械脱水处理(卧螺离心机),因来泥为各污水处理设施排泥,污水本身水质变化较大,所以污泥性质不稳定。其中,重力浓缩日处理量为2500m³~7200m³,离心机日处理量约为360m³~960m³。
2 离心机在试验和试运行期间的运行情况
2.1 卧螺离心机的技术参数及工作原理
该公司采用的是LW530×2270NY型卧式螺旋卸料沉降离心机。该离心机具有输出扭矩大,差速自动反馈调节,推料功率自动补偿,不易发生堵料情况,分离效率高的特点。
主要技术参数为转鼓直径530mm;转鼓有效工作长度2270mm;分离因数2200g;锥角2×8°;转鼓与螺旋差转速2~16r/min;转鼓转速0~2700r/min无级可调;悬浮液处理能力15~40m³/h;电机功率37kW;螺旋形式为单头、左旋、超前;转鼓形式:圆柱-圆锥形;溢流板直径为Φ283、Φ288.5、Φ294、Φ299.5四档可调。
工作原理是通过转鼓与螺旋的差转速△n实现固液的高效分离。
2.2 试验期间运行分析
2008年10月底,该公司选用LW350型卧螺离心机对循环水污泥进行了定性试验,LW350型离心机的主要参数为螺旋差速2~20r/min,转鼓转速3700r/min、电机功率15kW。絮凝剂选用浓度为1.5‰的阴离子型聚丙烯酰胺,试验数据如下:
试样 | 离心机参数 | 污泥参数 | 分离效果参数 | |||||||||
总电流/A | 差速/r/min | 转速/r/min | 液压扭矩/kg | 流量/m³/h | 含固率/% | 浊度/mg/l | 液固比 | 加药量/m³/h | 滤液液固比 | 滤液浊度/mg/l | 泥饼含固率/% | |
1 | 23 | 16.4 | 2940 | 24 | 4.2 | 16.76 | 6556.67 | 17:1 | 0 | 156:1 | 969.32 | 59.97 |
2 | 22 | 7.1 | 2690 | 27 | 5.7 | 9.27 | 9776.17 | 12:1 | 0.3 | 348:1 | 94.21 | 42.56 |
3 | 22 | 7.1 | 2690 | 27 | 5.7 | 9.27 | 9776.17 | 12:1 | 0 | 54:1 | 5979.9 | 31.48 |
4 | 22 | 9.5 | 2690 | 13 | 6 | 1.96 | 655.38 | 152:1 | 0.7 | 394:1 | 23.8 | 44.68 |
5 | 22 | 7.0 | 2690 | 18 | 5.5 | 3.01 | 7458.8 | 17:1 | 0.5 | 941:1 | 37.87 | 30.20 |
6 | 22 | 8.3 | 2690 | 39 | 7.0 | 9.27 | 7749.76 | 12:1 | 0.6 | 334:1 | 103.01 | 43.16 |
(1)在污泥参数基本相同的情况,差速越大,泥饼在离心机中停留时间也越短,泥饼含固率越低,相应的固体回收率也越低。
(2)对比第2组和第3组数据,在离心机参数及污泥固体总量一定时,加絮凝剂调节后,滤液浊度明显降低,固体回收率提高了20%,脱水性能得到改善。
(3)因污泥黏度小、碱性大,絮凝剂的用量较多,按进机污泥与加药瞬时流量的对应关系,假设进机污泥性质稳定,连续运行下,日均消耗1.5‰的絮凝剂约0.128kg/m³(泥),加药成本为5.1元/m³(泥)(絮凝剂按40元/kg计)。
2.3 试运行分析
2009年4月24日,新建卧螺离心机项目投入试运行。
因前期试验时加絮凝剂成本太高,且公司循环水污泥为无机污泥,成分复杂多变,泥沙含量大,同时含有铝、铁、钙、钠、钾等金属离子,黏性小,碱度大,悬浮物含量高,所有项目没有安装加药系统。
试运行期间,进机污泥参数变化不大,离心机的各项参数基本保持为污泥流量20m³/h、差速8r/min、转速1800r/min、主机电流30A,试运行数据如下:
试样 | 进机污泥参数 | 滤液参数 | 泥饼参数 | |||||
液固比 | 浊度/mg/l | 含固率/% | 液固比 | 浊度/mg/l | 含固率/% | 液固比 | 含固率/% | |
1 | 13:1 | 16535.71 | 7.38 | 31:1 | 6866.03 | 3.09 | 0.8:1 | 55.63 |
2 | 23:1 | 10990.85 | 4.16 | 55:1 | 5706.19 | 1.80 | 0.9:1 | 53.57 |
3 | 10:1 | 18558.77 | 8.75 | 31:1 | 8706.29 | 3.17 | 0.7:1 | 58.36 |
4 | 14:1 | 13894.68 | 6.55 | 52:1 | 8857.21 | 1.90 | 0.6:1 | 62.17 |
5 | 20:1 | 12916.33 | 4.68 | 42:1 | 9246.21 | 2.33 | 0.8:1 | 55.14 |
6 | 19:1 | 9371.10 | 4.91 | 39:1 | 8982.10 | 2.51 | 0.8:1 | 54.41 |
7 | 13:1 | 15755.11 | 7.31 | 30:1 | 10614.73 | 3.27 | 0.9:1 | 51.80 |
8 | 27:1 | 9580.56 | 3.52 | 55:1 | 4647.17 | 1.79 | 0.9:1 | 52.65 |
9 | 15:1 | 15072.09 | 6.44 | 36:1 | 11849.51 | 2.70 | 0.7:1 | 62.72 |
10 | 26:1 | 7076.14 | 3.67 | 66:1 | 5110.33 | 1.49 | 0.9:1 | 51.53 |
根据上表数据可知,离心机参数一定时,泥饼含固率随污泥浓度的升高而降低,在不加絮凝剂的情况下,泥饼含固率均大于50%,相应的固体回收率约为60%左右,每天外送干泥约20吨;脱水处理后的滤液浊度太高,因离心机的分离范围有限,大量的小颗粒在没有絮凝剂的作用下不能有效地脱除,溢流到下水道后进入污水处理系统,直接影响了循环水的水质(循环水供水主要控制浊度)。
3 问题分析及优化方案的选择
3.1 絮凝剂的取舍
因污泥本身浊度较高、固体颗粒比重小且属于难分离物料,絮凝剂的投加量会很大,同时形成的絮团强度不够,在重力浓缩阶段加入絮凝剂可以极大地减少进离心机的污泥量,但是进入搅拌槽后,在连续强力搅拌下,絮团极易破碎,容易造成后续投加絮凝剂过量。投加絮凝剂成本太高,不利于经济运行。
3.2 改变离心机滤液排放流程
流程改造方案为将滤液收集到溢流水箱,通过溢流水泵排至16米沉降槽。
3.3 优化重力浓缩处理流程
在机械脱水前,有两级重力浓缩处理设施,水处理西站的排泥连续且泥量较多,经过16米沉降槽一级浓缩处理后,进入3#、4#浓缩槽进行二级浓缩处理,且大泵房系统的排泥间断性进入3#、4#浓缩槽。
为较大限度利用两级重力浓缩处理设施,改变运行方式为在大泵房不排泥时,16米沉降槽底流排泥量为50m³/h;大泵房排泥时,大泵房排泥量限定为20m³/h、16米沉降槽底流排泥量为30m³/h。因为大泵房处理蒸发循环水,水源较少,水处理西站回水复杂,外来水源较多,沉淀池中污泥量较多,所以应压低大泵房的排泥,压低总排泥量,延长污泥在浓缩槽内的停留时间(12~16小时)。这样不仅可以保证浓缩槽的溢流水质,确保污泥的有效浓缩时间,尽可能降低污泥中的空隙水,提高进离心机的污泥含固率。同时可以减少进机泥沙含量,降低滤液的含固率,进而确保离心机的机动平衡。
3.4 合理化离心机运行参数
在参数的摸索调节中,转鼓转速过大会造成离心机本体的磨损和增加动力消耗,转速过小,达不到处理效果,在前期运行转速1800r/min的情况下,适当调节到2100~2500r/min范围内;同时结合污泥含固率的减少和物料的难分离特性,将差速由前期的8r/min降低到2.5~6r/min范围内,延长固体颗粒在离心机内的停留时间。调节后运行数据如下:
日期 | 离心机参数 | 污泥参数 | 分离效果参数 | |||||||||
总电流/A | 差速/r/min | 转速/r/min | 液压扭矩/kg | 流量/m³/h | 含固率/% | 浊度/mg/l | 液固比 | 加药量/m³/h | 滤液液固比 | 滤液浊度/mg/l | 泥饼含固率/% | |
5-18 | 32 | 6.4 | 2180 | 22 | 24 | 3.07 | 7954.31 | 32:1 | 0 | 50:1 | 6796.42 | 50.14 |
5-21 | 35 | 6.4 | 2180 | 23 | 24 | 2.20 | 6355.39 | 44:1 | 0 | 65:1 | 7054.67 | 46.01 |
5-24 | 46 | 6.4 | 2180 | 23 | 29 | 1.74 | 5431.02 | 57:1 | 0 | 69:1 | 5077.80 | 52.77 |
5-27 | 46 | 6.4 | 2180 | 25 | 30 | 1.54 | 4322.57 | 64:1 | 0 | 86:1 | 4812.40 | 41.73 |
5-30 | 46 | 4.1 | 2440 | 36 | 30 | 1.69 | 5889.63 | 58:1 | 0 | 74:1 | 6377.50 | 41.59 |
6-2 | 50 | 2.6 | 2440 | 54 | 30 | 1.52 | 5495.42 | 65:1 | 0 | 83:1 | 5567.63 | 48.32 |
4 阶段性效果及下一步运行要点
4.1 阶段性效果
结合上表的数据可以看出,随着进机污泥含固率的降低,通过适当增加转鼓转速和减小差速,经过离心脱水后的滤液液固比基本保持在80:1,泥饼含固率在48%左右,但相应的固体回收率低于50%。
下表为5月底每天的输送泵外排污泥量:
日期 | 5-23 | 5-24 | 5-25 | 5-26 | 5-27 | 5-28 | 5-29 | 5-30 | 累积量 |
外排泥m³/d | 8 | 9 | 15 | 31 | 8 | 11 | 12 | 9 | 103 |
干泥量t/d | 3.22 | 4.62 | 3.59 | 12.53 | 2.81 | 6.91 | 5.96 | 4.34 | 43.98 |
由上表数据可知,现阶段日均外排泥量为103/8=12.9m³,循环水系统日均可减少43.98/8=5.5t干泥,从根本上可确保循环水的供水水质。
4.2 下一步离心机的运行要点
(1)以设备安全经济运行为出发点,在保证泥饼含固率的基础上,调高溢流板的直径,适度降低差速,合理控制转鼓转速,尽量减少滤液含固率,提高固体回收率,通过有计划的实验寻找离心机的较佳经济运行点,并设计出不同条件下的差速变化曲线,指导离心机的运行。
(2)继续摸索重力浓缩处理系统的运行,结合进机污泥含固率持续低值的现状,间断运行排泥,即缩短排泥时间,增加排泥频次,延长污泥的浓缩时间,减少进离心机污泥的泥沙含量,保证进离心机的污泥具有较高浓度,确保离心机充分发挥脱水性能。
(3)加强离心机系统的运行维护,形成一套严格有效的管理制度,对关键设备或关键部件进行定期维护,确保系统的良好运行状态。