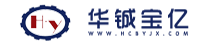
1 前言
鞍钢西区新2#、3#高炉的瓦斯泥采用集中处理,新4#、5#高炉煤气的洗涤采用了布袋式干洗除尘,新1#、7#、10#、11#高炉的瓦斯泥由给水厂36#水站送齐选过滤间进行处理。由于齐选过滤间的真空过滤机是处理精矿的设备,不适用于处理高炉瓦斯泥,造成未处理完的瓦斯泥排放至南大沟,导致南大沟水排入运粮河悬浮物超标,严重污染了辽河的水质。而且,瓦斯泥中含铁量在30%~40%,造成资源的严重浪费。经过比较污泥处理的各种工艺和设备,该厂决定尝试使用进口卧式离心机来实现瓦斯泥的脱水处理,这在国内同行业中尚属首次。为此,该厂将环水作业区现有的十二格沉淀池南三格填平,在此位置上新建了一座三层的污泥脱水间,内设4台进口卧式离心机、2个泥浆储罐、4台进料泵、2套PAM加药设备等。同时,更换了36#水站小泵房内送泥泵、新建和更新了各类配套管道。
2 卧式螺旋离心机的工作原理及运行管理
2.1 工作原理
卧式螺旋离心机是一种螺旋卸料沉降离心机。主要由高转速的转鼓、与转鼓转向相同且转速比转鼓略低的带空心转轴的螺旋输送器和差速器等部件组成。当要分离的悬浮液由空心转轴送入转筒后,在高速旋转产生的离心力作用下,立即被甩入转鼓腔内。高速旋转的转鼓产生强大的离心力把比液相密度大的固相颗粒甩贴在转鼓内壁上,形成固体层(因为环状,称为固环层);水分由于密度较小,离心力小,因此只能在固环层内侧形成液体层,称为液环层。由于螺旋和转鼓的转速不同,二者存在有相对运动(即转速差),利用螺旋和转鼓的相对运动把固环层的污泥缓慢地推动到转鼓的锥端,并经过干燥区后,由转鼓圆周分布的出口连续排出;液环层的液体则靠重力由堰口连续“溢流”排至转鼓外,形成分离液。
2.2 运行管理
由于该系统为高炉煤气洗涤水污泥处理系统,其回收水质变化大、污泥颗粒对设备磨损严重,且外界影响不确定因素多,再加上系统的处理设备种类多、处理环节交错,对运行操作人员要求较高。因此,要确保各环节的正常运行,充分发挥各设施设备的作用,就必须加强日常运行管理,要有一套管理措施来加以保证。具体概述如下:
2.2.1 督导运行管理人员搞好日常运行。熟悉各设施设备的功用,处理好各个环节的节点,加强工序间的协调。
2.2.2 根据瓦斯泥的泥质和泥量,抓住离心机运行的关键环节:
(1)进泥量的控制是卧式螺旋离心机运行的主要因数。
离心机有一个极限进泥量和极限入流固体量,实际进泥量超过该值时,离心机将失去固相和液相的动态平衡,扭矩过大,严重时会受到损坏,使离心机超载而停车,因而运行中应严格控制卧螺机的进泥量及入流固体量。选择适当的进料流量的方法:首先将进料流量调到较小值(变频控制下,一般调到60%~70%),然后启动卧螺机并工作一段时间,至固相出料的速度一定。在离心机入口处取样500mL,测定泥浆的沉降比,5min内沉淀在100~150mL处为正常,否则,开启旁通阀门,降低入料的浓度。
(2)离心机螺旋与转鼓的转速及其转速差的控制是离心机正常运行的关键
①离心机的转鼓是由变频器来驱动,转鼓的转速能在较大范围内无极调节,通过调节转速,可以控制离心机分离因数,使之适应不同分离液的要求。分离因数是离心机分离能力的主要指标,分离因数越大,物料所受的离心力越大,分离效果越好。离心机在运动过程中产生的离心加速度和重力加速度的比值,称为该离心机的分离因数Fr。
Fr=rw2/g,w=2πn/60。w是转鼓的角速度,n是转鼓的转速。
从公式中可以看出分离因数与离心机的转鼓半径成正比,与转鼓速度的平方也成正比,因此提高转鼓转速比增大半径对分离因数的影响要大得多。
通常分离液中固相颗粒越大,密度越大,需要较低的分离因数,反之则需要较高的分离因数。随着转鼓转速的上升,分离因数上升,分离效果提高,螺旋与转鼓之间的差转速随之增大,处理能力加大,但离心机的振动、噪声也随之增加,使用寿命会有所下降,生产运行的经验认为,将转速控制在2000~2300r/min。
②转速差是指转鼓与螺旋的转速之差,即两者之间的相对转速
如果转速差为△n,则螺旋相对于转鼓来说,等于以△n的速度在旋转,液环层中被分离出的污泥就是利用这个速度被输送出脱水机的。当进泥量一定时,转速差越大,污泥在脱水机中停留的时间越短,固环层就越薄。另一方面,转速差越大,由于转鼓与螺旋之间的相对运动增大,使得对液环层的扰动程度增大,固环层内一部分被分离出来的污泥会被重新泛至液环层,并有可能随分离液流失。转速差增大时,脱水的固体回收率和泥饼的含固量都将降低,但增大转速差可提高离心机的处理能力。减小转速差时,污泥在转鼓内接受离心分离的时间将延长,同时由于转鼓和螺旋之间的相对运动减小,对液环层的扰动也减轻,因此固体回收率和泥饼含固量均将提高。但减小转速差,往往使处理能力降低,转速差不能太小,否则将由于污泥在机内积累,使固环层厚度大于液环层,导致污泥随分离液大量流失,固体回收率急剧下降,严重时还会由于阻力过大,扭矩超负荷损坏离心机。根据时时监测入泥的浓度(一般按照五分钟沉降比来计算,即取500mL水样,5min沉淀量),来调整转速差。当沉降比在10%~20%时,转速差调至30r/min,当沉降比在20%~30%时,转速差调至30~34r/min,当沉降比更高时,调整入水浓度。
(3)液环层厚度的调整是离心机运行的重要环节
当进泥量一定时,液环层越厚,污泥在液环层内进行分离的时间越长,会有更多的污泥被分离出来。液环层增厚一般会提高脱水的固体回收率。但液环层增厚,相应会使干燥区缩短,使脱离液环层的污泥没有充足的时间被“甩干”,因此泥饼含固量将下降。但液相端的出水含固率会下降,通过调整液相出口堰板的高度来调整液相环的厚度。
(4)运行中出现的现象与调整方法
现象1:分离液混浊,固体回收率降低。
调整方法:
①液环层厚度太薄应增大厚度。
②进泥量太大,应降低进泥量。
③转速差太大,应降低转速差。
④入流固体超负荷,应降低进泥量。
⑤螺旋输送器磨损严重,应更换。
⑥转鼓转速太低,应增大转速。
现象2:泥饼含固量降低
调整方法:
①转速差太大,应减小转速差。
②液环层厚度太大,应降低其厚度。
③转鼓转速太低,应增大转速。
④进泥量太大,应减小进泥量。
⑤调质加药过量,应降低干污泥投药量。
现象3:转轴扭矩太大。
调整方法:
①进泥量太大,应降低进泥量。
②入流固体量太大,应降低进泥量。
③转速差太小,应增大转速差。
④齿轮箱出故障,应及时加油保养。
现象4:卧螺机过度震动
调整方法:
①润滑系统出故障,应检修并排除。
②转鼓内部由于冲洗不干净,造成转动失衡,应停止进泥,并用清水进行清理。
③机座松动,应及时修复。
现象5:能耗增加,电流增大。
调整方法:
①如果能耗突然增加,则可能卧螺机出泥口被堵塞。停机后进行清理。
②如果能耗逐渐增加,则可能转鼓与机壳之间积累了一定的污泥,从而阻碍了转鼓运行。
(5)加药控制是提高离心机脱水能力的重要手段
物料中固相粒子越大,液固两相的重度差越大,悬浮液的粘度越小,则越易分离;反之,则越难分离。为此在悬浮液进入卧螺机之前,可采用通过添加絮凝剂使固相凝聚等预处理手段来改善分离条件。通过工业试验,阴离子型分子量大于1200万的聚丙烯酰胺较理想。投加方式为自动投加:药剂经过螺杆泵→提升泵出口→离心机入口。
影响絮凝效果的因素还有药剂的配置浓度和添加量。通常,泥浆浓度高时,药剂配制的浓度可相对低些,反之亦然。对于高炉煤气洗涤水经两次浓缩后的污泥,浓度在10%左右,药剂的浓度配成0.25%较好,投加量为1.2~1.5kg/t污泥。离心脱水一般采用高效的人工合成高分子絮凝剂,而不采用无机盐类混凝剂。其原因是添加无机类混凝剂会使得污泥体积膨胀,而离心机为封闭式强制脱水,对进泥量有较严格的要求,因此如果采用无机盐类混凝剂会使离心机的脱水能力大大降低。
3 存在的问题及改进措施
3.1 投产初期存在的问题
该系统从2008年10月开始投产,在运行初期中,发现局部存在一些设计与工艺不符的现象,严重影响生产运行,维修频繁,设备设施难以管理,主要变现在:
3.1.1 系统经二次浓缩后的污泥浓度偏高,与设备的参数存在差异。
3.1.2 设备的入泥管道口处的挡板经常出现断裂,高速运行的离心机被迫停机,造成离心机内部的筋条断裂。
3.1.3 提升螺杆泵的运行效率逐渐降低,定子和转子均出现磨损,出水量降低到设计流量的1/3~1/4,流速降低,管道极易堵塞,造成浓缩机负荷增大,刮泥耙子被泥压住。
3.1.4 离心机出泥口的设计不利于现场取样及运行观察。
3.1.5 泥斗间的设计不利于出泥,经常造成出泥不畅而堵死出泥口,设备被迫停机的现象。
3.1.6 离心机的润滑点设计不合理,特别是刮板机轴承处的润滑点,没有保护,被泥封死,不利于润滑。
3.1.7 固相出泥口侧污泥极易渗入转鼓与离心机壳之间,造成大量积泥,严重影响设备运行。
3.2 改进措施
3.2.1 在污泥上料罐处、螺杆泵污泥入口处安装DN80mm净环水管道,稀释入料的浓度,并在入料罐至螺杆泵之间的管道两端,安装DN80mm的冲洗管道及DN100mm的放水管道,避免堵塞。
3.2.2 更改离心机入泥管道口的设计,废除挡泥板。
3.2.3 更换提升螺杆泵为渣浆泵,彻底解决提升泵效率低的弊端。
3.2.4 更改出泥口的设计,改不锈钢刚性出泥口为挂胶帆布材质的布袋式出泥口,便于取样与运行观察。
3.2.5 在泥斗间制作刮泥平台,解决拉泥车由于空间的制约而无法装运的难题。
3.2.6 更改润滑点处的设计,对易堵塞的润滑点加保护装置,防止堵塞。
3.2.7 在离心机入口管道处,增加一条DN80mm的净环水管道,解决离心机开机时的振动和停机时的反冲洗问题,为避免转鼓与离心机壳之间积泥,压力控制在0.2~0.21MPa。
4 运行效果及经济效益
污泥处理系统改进后,合理调整离心机的运行参数,避免了设备故障停机及管道污泥堵塞,节省了备件及检修费用,降低了运行人员的劳动强度。在达到环保目标的同时,干污泥的回收又创造了一定的经济效益。经济效益的计算如下:
目前10#高炉已停产准备改造,集中处理的三座高炉煤气洗涤水的总水量为3800m³/h,平均悬浮物含量以2000mg/L计,则每小时产生的绝对干泥量=3800×2000÷1000000=7.6t/h。若污泥含固率以60%计,则每年将产生的需装车外运的污泥量=7.6÷60%×24×360=10.944万t。炼铁厂回收此瓦斯泥的价格为50元/t,则年产生经济效益:10.944×50=547.2万元。该项目的一次性投资近1700万元,大约3年即可收回投资。
5 结束语
经过生产实践,利用卧式离心机进行高炉煤气洗涤水的污泥处理比带式压滤机有很多改进和提高,现场环境整洁,工人劳动强度大大降低,保证了鞍钢大高炉生产的稳定,为公司创造了较大的经济和环保效益。同时,还在国内首家使用了卧式螺旋离心机用于高炉煤气洗涤水污泥的处理,积累了运行经验。但是,由于高炉回水悬浮物变化大、水质含量复杂等因素的影响,在设备选型的过程中,需要根据实际情况,进行工业试验,并通过采取有效的措施去解决生产实际问题,把高炉煤气洗涤水污泥处理工作推向深处。