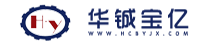
1 污泥来源及污泥性质
1.1 污泥来源
2008年,大庆油田采油五厂污泥产生总量为10362t,其中转油站清罐污泥第二季度2256t,第三季度97t;脱水站清罐污泥第二季度131t,第三季度225t,第四季度1495t;污水站清罐污泥第二季度76t,第三季度1916t,第四季度33t;深处理站清罐污泥第三季度3670t;井场落地油泥第一季度63t,第二季度279t,第三季度44t,第四季度77t。
1.2 污泥性质
油田含油污泥的组成成分极其复杂,一般由水包油、油包水及悬浮固体杂质组成,是一种极其稳定的悬浮乳状液体系,含有大量的老化原油、蜡质、沥青质、胶体、固体悬浮物、细菌、盐类、酸性气体、腐蚀产物等,还包括生产过程中投加的大量絮凝剂、缓蚀剂、阻垢剂、杀菌剂等水处理剂。另外,大庆油田实施聚合物驱三次采油,油田聚合物含油污泥所含化学成分中还包含弱酸低温胶联剂、聚丙烯酰胺硫化物等。油泥在水中一般呈稳定的悬浮乳状液体系,由于其带电性形成了稳定的分散状态,很难实现多相分离,从而增加了处理技术的难度和成本。
从运行情况来看,清淤所出的含油污泥中含水率较高,综合含水率大于80%,一些似油非油的物质也占相当比例,油、泥所占比例则较小。处理后的污油凝固点较高,且电导率较高,影响电脱水器的正常运行。
2 工艺描述
采油五厂含油污泥处理总体工艺流程如下:含油污泥→污泥流化预处理→调质→离心分离处理。该工艺以物理、化学法相结合的离心分离为主,充分重视含油污泥的预处理,确保处理后污泥中的含油量≤2%,达到环保要求。
(1)第一步:流化和预处理。由于含油污泥的来源广,成分复杂,污泥中所含的杂质种类多,因此在含油污泥进入调质-机械脱水的主工艺之前,需要将大块的固体杂质从污泥中去除,减少后续机器的磨损并保证其处理效率。另外,在该工序中,通过加入回掺热水(系统循环利用的水),可将污泥升温至45℃,并将含固量较高的污泥流化成含固量在15%左右的可流动的污泥。其工艺流程为从污泥池中或罐车收取的固态、半流态和流态的污泥,用吊车直接送至污泥流化和预处理装置进行处理,分选出的大块杂质经充分清洗和处理后,用螺旋输送机送至翻斗车,液态含油污泥进入调质罐进行调质。
(2)第二步:污泥调质。黑色粘稠含油污泥浓缩液一般由水包油(O/W)、油包水(W/O)及悬浮固体共同组成,属于多相的胶体体系,组成较为复杂。由于含油污泥颗粒表面吸附同种电荷,相互之间排斥,加之充分乳化,极难脱稳,使得油、水、泥渣分离比较困难。需要加入调质剂,使原油与固体颗粒分离、油滴聚合、原加入的化学药剂随固体杂质沉降,实现油、水、渣三相的完全分离。实现液-固分离的关键是使黏度大的吸附油解吸或破乳,为促使油类从固体离子表面分离,对污泥进行调质处理,对污泥进行进一步的加热和匀化,为油从固体颗粒表面脱附创造更好的条件。目前投加的药剂为调节剂、清洗剂和破乳剂。
(3)第三步:含油污泥的机械分离。分离出的液体进入油水分离装置,分离出的油被回收,分离出来的水进回掺水罐作为工艺用水循环利用,多余的水回来料池再处理。分离出的污泥用于铺路或对其进行深度处理。
3 运行情况及存在的问题
3.1 运行状况
2008年5~8月,采油五厂含油污泥处理情况如下;5月份主要处理2007年污油收集池剩余的油泥和作业清池油泥,运行效果较好,不外输污水,每天外输污油控制在5m³以内,对杏五二联合站系统运行影响较小。6月中旬清淤送料增多,每天外排污水30m³左右,外输污油控制在8m³以内(包括经保的油),联合站系统开始明显波动,系统不稳的时候减少或停输油、水,联合站系统和污泥处理基本能维持运行。7月份送料增多,每天外输水100m³左右,外输污油控制在8m³以内(包括经保的油),联合站系统运行开始不稳定,油系统电脱水器不稳定,水系统水质变差,联合站系统开始限制水、油的外输。8月份尝试水不进污油池,直接进外输管线,外输油和提捞油掺在一起外输,没有明显效果。8月24日起油、水均停输,8月29日外输油进作业罐车用于调剖,8月30日磁处理开始处理污泥收集池中沉降的污水,基本能达到“双20”指标,8月30、31日两天外输110m³水,联合站系统运行正常。
3.2 存在的问题
3.2.1 实际处理能力偏小
虽然离心机的设计处理能力为10t/h,但在流化预处理时需要8~9倍油污量的循环掺水冲洗油泥中的杂质、颗粒,如果减小掺水量,则预处理所出的杂质会明显含油,而且掺水循环使用时的水质也会变差。单台离心机每天实际可处理的较稠含油污泥量为50~60m³。如果污泥收集池的水能沉降分离再经磁过滤处理后输送至游离水,将大幅度地提高岗位处理能力,但即使同时运行2台离心机也与240t/d的设计处理量有差距。离心机处理前含泥量≤15%,在实际运行中只有尽量接近15%,才能尽可能多地处理含油污泥。
3.2.2 设备问题
设备自投运以来主要存在以下问题:
(1)2台离心机漏油,虽然不影响正常生产,但德国工程师来现场后也未找出原因加以解决。
(2)1号离心机的油水混合泵泵效下降较多,厂家解释为定子磨损,需更换定子。
3.2.3 外输油的去向
目前,外输油每天通过罐车拉走一部分,剩余的溢流回收集池。但是罐车拉走的油有限,如果每天拉走的油量远小于送料带来的油量,则池中的油会越来越多。
4 建议
(1)进一步对油、水进行深加工处理。由于清淤产生的含油污泥中水所占的比例很大,而且水是回收进入系统的,所以对水进一步处理,把水中一些杂质水分清除再回收进入系统,既能提高池子的利用效率(及时把水沉降处理再外输),也能提高含油污泥的处理效率,还能很好地改善水质。目前,磁分离的运行基本能满足水处理的要求。同样,油如果能进行深处理,既能消除脱水器运行不稳定的可能,也对水质有益,还能带来经济效益。
(2)植物修复。目前,两相分离出的泥含油率<2%,仅能达到用于铺路和进场的标准。进一步深化处理可考虑将分离出的泥进行指定区域的土壤改良,将指定区域覆盖一定厚度的土,种植一些适合环境生长的植物,利用植物的根系吸附作用或者将植物和微生物联合修复,既进一步降低石油烃含量,使该土壤达到可以利用的目的。
(3)调剖回注。油田由于长期注水开发,每年都有大量注水井需要实施调剖作业。含油污泥本身主要由不同粒径的泥质颗粒加上部分油、水和其他杂质所组成。可以利用含油污泥作为原料,研制一种调剖剂,将含油污泥回注入地层,利用含油污泥中的污泥颗粒对地层的高渗带形成封堵,在有效环保处理含油污泥的同时实现对注水井的调剖作业。以国内西部油田为例,利用含油污泥作为调剖剂的原料,研制含油污泥调剖体系,使其能够回注入地层,并利用污泥颗粒对地层的高渗带形成封堵,在有效环保处理含油污泥的同时实现了对注水井的调剖。
(4)多种方法结合处理。从目前看,以离心分离技术为核心,多种预处理和后续处理技术相结合的工艺比较可行。尤其是国外普遍应用的机械脱水工艺,辅之以调制、倾析等预处理技术和高温裂解、生物处理等后续处理技术,比较适合我国现阶段和未来的污泥处理需要。结合国内实际情况,在引进和消化关键技术和设备的基础上已逐渐形成满足我国环保需要的含油污泥处理新技术。
(5)专业处理。国外含油污泥处理通常是由专业承包商来完成的,由于含油污泥收集、脱水、运输和处理操作难度大、技术含量高,且具有临时性及批量性的特点。因此从规模收益考虑,发展含油污泥处理的专业化服务产业在我国也是大有可为的。