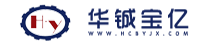
1 前言
粗液分离是氧化铝生产过程中的关键工艺,粗液分离效果的好坏,直接影响氧化铝回收率的高低。加快粗液分离速度,是减少溶出过程中的二次反应、提高氧化铝净溶直接的办法。
强化烧结法生产氧化铝过程中,如果能够较好地解决高浓度铝酸钠溶液与赤泥快速分离问题,则可以大幅度降低强化烧结法生产氧化铝的汽耗,大大提高熟料的氧化铝净溶,进一步降低生产成本,提高企业的市场竞争力。
为了加快分离速度,减少二次反应,在氧化铝行业曾先后用于分离的设备包括:沉降槽、过滤沉降槽、板框压滤机、带使和转盘真空过滤机等。现保留使用的设备仅为沉降槽,而其它设备均因存在工人劳动强度大、分离不均匀、洗涤不充分和滤布消耗量大等问题,而限制了这类设备产能的提高,从经济的角度来看,不适应氧化铝生产的不断扩大。在合成高效絮凝剂等添加剂出现后,沉降槽的产能有了较大提高,但中国铝业中州分公司在使用强化烧结法生产工艺后,熟料中的A/S有了很大提高,赤泥的细度也相应减小,对粗液分离提出了更高的要求。为了适应强化烧结法生产工艺的要求,须寻求一种更为先进的分离设备。
2 设备选型
卧螺离心机是现今在水处理行业应用较为有效的设备之一。经过调研和分析,该公司选用上海离心机研究所生产的LW530×2270NY型离心机作为分离设备,进行高浓度下的快速分离试验。
2.1 设备结构
LW530×2270NY型卧式螺旋卸料离心机由转鼓、螺旋、液压差速器、液压泵站、液固相收集腔、电机传动装置和变频器等构成。
2.2 工作原理
启动液压电机,使转鼓与螺旋产生差速,通过主机变频器逐步升速到额定转速,在液压差速器的作用下,使螺旋产生一个超前转鼓的稳定差速器,以实现螺旋的卸料功能。
机器转速稳定后,悬浮液由进料管进入离心机,在强大的离心力场作用下,比重大的固体离子被甩在沉降壁面上,并很快沉积在转鼓的内壁上,在螺旋的推动下,沉渣不断被推向转鼓的小端,从出渣口排出。清液经分离叶片进一步澄清后,由转鼓溢流孔排出。在整个分离过程中,悬浮液不断地输入,澄清的液相不断排出,从而实现了连续自动分离。
2.3 设备性能参数
卧式螺旋卸料离心机适用于分离固相含量<10%,液固体积浓度<50%,液固重度差>0.05g/cm³,固相离子直径>5μm的悬浮液。当液固重度差较大时,固相粒子直径>2μm的悬浮液也可以分离。
粗液的比重一般为1.2~1.25g/cm³,赤泥的比重为2.79g/cm³,重度差为1.57g/cm³,赤泥的粒度分布-5μm是19.9%,-2μm是10.79%。因此在离心分离机的适用范围内,可以进行离心分离。
3 试验过程及结果
3.1 实验目的
检验离心分离机应用在烧结法粗液、赤泥快速分离上的可行性,包括离心机连续稳定运行的周期、结疤对设备的影响情况、设备的产能以及设备的可靠性等。
3.2 试验结果
将溶出浆液直接送入离心分离机进行分离,以分析其稳定运行的作业条件和产能大小。经过591h的运行,期间共停车15次,经过两次大修。
3.2.1 结疤情况
试验机内的转鼓分三段:清液区、进料区和排渣区。其中清液区的结疤形状为:转鼓内结疤8~10mm,螺旋结疤3~5mm,呈深蓝色。进料区:转鼓内结疤8~10mm,螺旋结疤3~5mm,呈褐色。
进料管亦存在一定程度的结疤,但在试验中,并未发现离心机的振动加剧。因此可以认为:采用卧螺离心机进行粗液分离,结疤对设备运转的影响可以忽略。
3.2.2 可维修性
在试验中,曾由于操作不当造成离心机堵塞,进行过两次解体大修,对其中的积料和结疤进行了彻底清理。再次安装后,设备运行平稳,未出现因检修而致设备停运的情况。
因此,可以认为,检修工作只要按照设计和检修规程执行,该设备仍具有一定的可维修性。
3.2.3 工艺指标
试验机的设计产能为30m³/h。当离心机的进料量稳定在13.5~17m³/h、平均为14m³/h时,溢流浮游物平均为0.66g/l,底流水份平均为39%。离心机试验底流赤泥氧化铝溶出率平均为94.4%,与同期沉降槽底流氧化铝溶出率93.47%相比,提高0.97%;当离心机的进料量稳定在25~35m³/h,平均为30m³/h时,溢流浮游物平均为1.44g/l,底流水份平均为40%。离心机试验底流赤泥氧化铝溶出率平均为95.37%,与同期沉降槽底流氧化铝溶出率93.04%相比,提高2.33%。
3.2.4 絮凝剂对工艺指标的影响
为提高产能加入适量的絮凝剂后,离心机的进料量可由35m³/h提高至45m³/h,平均为39.6m³/h。絮凝剂的加入量低至160~200ml,为干赤泥量的0.05‰;高至350~500ml,为干赤泥量的0.18‰。溢流浮游物平均为1.92g/l,底流水份平均为37.12%。底流赤泥氧化铝溶出率平均为95.81%,与同期沉降槽底流氧化铝溶出率92.20%相比提高了3.61%。
4 试验机存在的问题
从试验过程来看,工艺指标达到了预期的目标,离心分离后,粗液浮游物平均为1.61g/l,氧化铝溶出率平均为95.29%,与同期沉降槽底流赤泥相比,氧化铝溶出率提高2.33%;但设备本身仍然存在诸多问题。
4.1 轴向密封效果差,轴承损坏
试验中因轴承损坏,曾造成两次停机检修。
现有的设备结构并未考虑轴向密封问题,只是在壳体的两端采用了毛毡密封,这对易结硬的物料基本上不起作用;同时,这种结构也不利于对物料的密封。
4.2 出渣口易堵塞,不利于出料
由于氧化铝赤泥的粘度大,易结硬,因此,排出的渣应迅速脱离设备。试验中,经常因出渣排出不及时造成堵塞。
4.3 保护罩上未设置出气筒,护罩内的废气难以排出
流程中的物料温度在80℃左右,其产生的废气无法排出,依靠密封亦难以完全封死,造成传动系统污染,易出故障。
4.4 进料口易磨损
由于进料部位的结构为垂直出料,造成物料反射,使进料口磨损严重,因此会降低设备的使用寿命。
4.5 未设溢流装置
试验中进料量波动,进入分离机的物料有时大于设定的产能,形成进料口倒料。试验机对物料波动特别是进料量大于设计产能时的情况,没有应对措施,造成环境污染。
4.6 部件拆卸不便
转鼓的连接法兰因位置小,不易拆检;差速器与螺旋轴的连接销轴亦不易拆除,拆检困难。
5 改进措施
尽管卧螺离心机能够获得较好的工艺指标,但其自身结构存在问题,需进行相应的改进。从试验过程可以看出,排渣口堵塞是造成设备停机较多、且较不易处理的故障。
为了能在生产中使用该设备,从烧结法物料的特性出发,结合该设备本身的结构特点,提出了以下改进措施。
5.1 改进密封结构
在两端的出料位置各设置一个挡料环,以加强轴向密封效果。
5.2 设计专门的挡料圈
在出渣口处设计专门的挡料圈,并在保护罩上设计洗液冲洗口,使泥渣能够及时排出,避免泥渣堵塞。
5.3 改造保护罩
将保护罩的下半部分改为斜斗形,并加冲洗管,以便及时冲洗里面的积泥;同时加上拔气筒,以排出保护罩内的热气;将保护罩上的加强筋板设置在外壁(原设计在内壁);清液出口加集料装置,结构类似出渣口,以减少物料外溢。
5.4 进料出口加防磨层
在螺旋中心的进料出口加防磨层,即在出口位置向前耐磨材料或对出口形状再做改进,以延长使用寿命。
5.5 设置溢流装置
为了应对由于进料量的波动、造成进入分离机的物料有时大于其设定的产能、出现出料口倒料的情况,设置溢流装置,在保证机器产能的前提下,可以自动分流。
5.6 加大连接法兰尺寸
转鼓的分体连接法兰适当加大,考虑螺栓连接或其他有利于拆卸的连接方式,至少在半径上增加30mm,可预留扳手转动空间,保证检修拆卸方便,可靠。
6 试验结论
(1)采用卧式螺旋离心分离机进行铝酸钠溶液与赤泥的快速分离,基本上可以达到快速分离的目的。
(2)离心分离后粗液浮游物平均为1.61g/l,氧化铝溶出率平均为95.29%,与同期沉降槽底流赤泥相比,氧化铝溶出率提高2.33%。
(3)在离心分离机相同的转速下,添加絮凝剂可以提高离心机的产能。该离心分离机的额定产能为30m³/h,添加絮凝剂时可以达到39.6m³/h,并且粗液浮游物平均为1.92g/l,氧化铝溶出率平均为95.81%,与同期沉降槽底流赤泥相比,氧化铝溶出率提高3.61%。
(4)离心分离机在额定流量和较低转速下运行比较稳定,但是,转速低导致浮游物升高。
(5)烧结法赤泥容易结硬,在如何解决排渣口结硬导致设备停机问题上,还需对排渣口做进一步的改进。