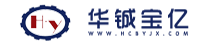
在石化行业,污水处理场的污泥主要是由“三泥”即油泥、浮渣和剩余活性污泥组成,此外还有少量污油罐的罐底泥和沉砂池的泥沙。如果处理不当,很容易造成二次污染。石油行业技术人员一直对炼油污水厂含油污泥的有效处理进行着不懈地探索。从上世纪70年代开始,对含油污泥的处理方法不断发展。起初用静置储存,自然沉降的方法进行处理,然后发展到用真空过滤机、板框压滤机处理,到现在利用卧式离心机进行处理。但卧式离心机在运行中会产生很多问题,如果不加以解决,处理效果很差,甚至不能进行有效的固液分离。文章对一些运行中的问题及解决办法进行讨论。
一、三泥的产生和特点
我国炼油污水在污水处理厂处理的同时,会产生“三泥”。“三泥”的主要来源是生化池内的污泥,浮选产生的浮渣、回收污油脱水产生的油泥、隔油池底泥的排放等,是石化工业的主要污染源之一。炼厂污泥含水率较高,活性污泥中含有毒有害物质较少,较易处理,浮渣含一定量的无机物(如铝盐)、水和油。炼油污水中污泥的含水率在60%~99%,其余的是固体物质如泥、砂、微生物胶团体、悬浮液和絮凝剂的聚合物等。
二、三泥的处理现状及难点
含油污泥是一种多介质的混合物混合在一起形成一种较稳定的悬浮液体。含油污泥首先可以通过静置沉降,将含油污泥中的水分离出来。剩下的悬浮液体中,由于有石油类物质粘附在固体颗粒上,而石油类物质又有很强的粘附力,因此形成了更为稳定的混合液体。这种混合液用静置沉降的方法处理效果很差。“三泥”机械脱水以带式压滤机,离心机为主,基本上淘汰真空转鼓过滤,板框过滤,这是由于黏度较大的油泥、浮渣、池底泥其中的油份容易堵塞滤布眼,使水分不能滤出的缘故。卧式离心机处理含油少的活性污泥效果良好,但是处理油泥和浮渣时,离心转速一般控制在1800~2000r/min,1800以下离心效果较差,2000r/min以上离心效果一般,但泥饼难以挤出,噪音大。经离心机脱水后,污泥的含水率在75%~80%之间。离心机处理浮渣时,经常会出现离心液偏黑的现象。浮渣在离心机转鼓的壁上沾黏性较大,导致部分浮渣无法刮出,会经常出现运行时振动大的问题,有时也会出现出料口堵塞的故障现象,影响离心机的正常运行。
三、离心机对三泥处理难题的对策
1. 加强离心机进料性质的分析,调整离心机运行参数
通过对故障离心机解体检查发现,造成振动大的主要原因是有些不均匀的污泥黏附在离心机转筒内,切换进料性质时,随着转筒转速的提高,转筒失去动平衡。有时勉强运行起来,使黏附的污泥从转筒上甩出,在机内输送螺旋的带动下,移动到出料口,如果污泥较多,就会产生出料口堵塞故障。产生不均匀污泥黏附的主要原因是长时间运行且对转筒水冲洗不彻底,有些黏度较大的污泥或浮渣没有被洗出来。通过多次试验,离心机处理浮渣时,要及时根据进料性质的变化,调整辅机的转速,扭矩等参数,并加强离心机的冲洗频次,离心机开启先空载运行,直至转速平稳,无振动超标后,继续运行,这样会提高离心机运行的稳定性。
2. 加大三泥的预处理力度,根据进料性质适当提高加药量
通过实际运行试验,将离心机的进料物质,经过简单的重力脱水后,含固量高的污泥进入离心机处理,初次处理能分离出大量干泥,离心液为黑色液体。将这种类似胶体溶液的黑色液体收集后再次经过离心机处理,可以产生大量清水。因此,对含固量高的污泥建议采用离心机处理,离心液收集,然后离心机再处理的二次处理法。两次处理的加药量不同,一般一次加药量要高于二次处理的加药量。
3. 通过调整离心机内溢流口的高度,改变离心机的性能
通过实际运行试验,通过调节离心机转鼓上的溢流口高低,从而来改变液池深度的大小,达到调整脱水段和沉降段的大小,通过此技术的调整,可以满足不同要求的分离效果。当离心机脱水段比较长,对提高泥饼干度有较大影响。反之,可以得到更高的上清液回收率。溢流口的调整往往都是根据离心机进料的性质来调整的,以便离心机在处理三泥时实现该功能的良好状态。
结论:根据上文所述,卧式离心机在三泥处理应用过程中,操作简便,设备运行稳定,处理效果显著。经过卧式离心机的脱水分离,可以减少三泥的体积,逐步实现“减量化,稳定化,无害化和资源化”的目标。