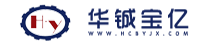
随着我国炼油厂处理原油性质的恶劣化,尤其是重质油、高酸原油的炼制,导致污水水质恶化,污水处理过程中产生的浮渣和油泥量大增。污泥的处置方式有2种:焚烧或作为危险废物填埋。为减少处置成本,脱水后的污泥含水率是污泥处理减容的一个重要指标,相对于目前在炼油厂污泥脱水中应用较多的离心脱水工艺,叠螺脱水机具有能耗低、运行效果平稳、噪音小等优点,在运行成本、操作管理等方面具有明显的优势。文中阐述和分析了离心脱水机和叠螺脱水机在工作原理、工艺流程和运行成本上的差别,以期为污泥处理设备的合理选择提供参考。
一、炼油厂污泥特性分析
1.炼油厂污泥来源
炼油厂污水处理场的污泥由油泥、浮渣和剩余活性污泥所组成,通常称为“三泥”。油泥包括污油罐底泥和池底泥,罐底泥是污油罐在加温脱水时,产生的油、水、泥等的混合物;池底泥是炼油厂含油污水在隔油池中进行油、固、水三相分离后,沉积在池底的油泥。浮渣来自于炼油厂含油污水处理的浮选池,剩余活性污泥来自于含油污水生化处理系统的二级沉淀池。
2.污泥的性质
油泥一般为由油、水、固体物质组成的稳定的悬浮乳状液体系,其中池底泥大部分为自然沉降的油粒、泥、渣、灰等,沉降性能较好;浮渣含有较多的污油、化学药剂和气泡;剩余活性污泥含有较多的微生物、细菌和较少的油,可挥发性固体含量约占总固体含量的80%。我国炼油污水处理过程中产生的浮渣在“三泥”中所占比例较大,其实是剩余活性污泥,油泥所占比例仅为10%左右。而炼油厂污泥处理中,一般是将油泥和浮渣混合后进行处理,其中主要成分是浮渣。
二、污泥脱水设备在炼油厂污泥处理中的比较分析
由于污泥的含水率比较高,直接排放会增加后续污泥输送设备的数量和污泥干化或焚烧处理成本,因此,需要对污泥进行脱水处理。目前在炼油厂污泥脱水处理中应用较多的是离心脱水工艺,叠螺脱水技术的应用时间较短,但因其在运行成本等方面的优势,目前正得以逐步推广使用。
1.工作原理比较
1.1叠螺脱水机工作原理
叠螺脱水机是运用了螺杆挤压原理,通过螺杆直径和螺距变化产生的强大挤压力,以及固定环与游动环之间的微小缝隙,实现对污泥进行挤压脱水的一种新型的固液分离设备。
叠螺脱水机主体是由固定环和游动环相互层叠、螺旋轴贯穿其中形成的过滤装置,它集浓缩和脱水为一体,前段为浓缩部,后段为脱水部。每个游动环都镶嵌在2个固定环中间,之间形成的滤缝从浓缩部到脱水部逐渐变小,螺旋轴的螺距从浓缩部到脱水部也逐渐变小。固定环的内径和螺旋轴的螺旋直径相同,游动环的内径小于固定环的内径,脱水部的终端有一个背压板。
叠螺脱水机主体采用倾斜安装或水平安装,脱水部处于后端。螺旋轴旋转带动游动环做圆周运动,由固定环和游动环组成的过滤结构便处于运动的状态,不易堵塞。水从滤缝中流出,起到了自我清洗的效果,污泥则被螺旋轴不停地向前推进。污泥在浓缩部经过重力浓缩和较小压力挤压后,被运输到脱水部,在前进的过程中,随着滤缝和螺距的逐渐变小,螺杆和滤缝挤压力逐渐增大,污泥浓度不断提高。背压板的阻挡作用产生极大的内压,将污泥中含有的少量水分挤出,污泥变成泥饼。
叠螺脱水机主要是依靠螺杆的挤压来实现污泥脱水,泥水密度差、含油量均不会对设备的处理效率产生影响,可以实现低浓度污泥的脱水。叠螺脱水机螺旋轴的旋转速率很低(约为2r/min),这决定了叠螺脱水机耗能低、无噪声、运行成本低等特点。叠螺脱水机采用全封闭箱体,箱体上有预留恶臭气体处理接口,可以有效地降低污泥中恶臭气体(如硫化氢)对周围工作环境的污染。
叠螺脱水机运用螺杆挤压原理对污泥进行脱水,颗粒大、硬度大的污泥会使螺旋轴、游动环和固定环之间产生大的磨损。随着运行时间的延长,螺旋轴的螺距和游动环与固定环之间的微小缝隙会变大,螺杆和滤缝产生的挤压力会减弱,这样会降低污泥脱水效果。一般滤缝变大后可以通过调节螺杆自锁螺母重新上紧,如发现有磨损情况,可视严重程度决定是否用打磨设备打磨或者更换环片。因此,该设备不适用于含较大硬度颗粒,尤其是含大量砂石、大的金属类物质的污泥脱水。
1.2离心脱水机工作原理
离心脱水机是利用转鼓高速旋转产生的离心力进行固液分离的一种传统污泥处理设备。
离心脱水机由转鼓和带空心转轴的螺旋输送器组成。污泥由空心转轴送入转筒,在高速旋转产生的离心力作用下,立即被甩入转鼓腔内。由于泥水密度不一样,形成固液分离。污泥在螺旋输送器的推动下,被输送到转鼓的锥端由出口连续排出。液体则由堰口连续“溢流”排至转鼓外靠重力排出。
离心脱水机主要是依靠泥水的密度差来实现固液分离。决定设备脱水效果的关键是泥水的密度差,油泥、浮渣及剩余活性污泥与水的密度差均不大,而且油泥、浮渣的含油量很高,这些因素增加了离心脱水机处理含油污泥(主要成分是浮渣)的难度。为了提高泥水分离效果,需向离心脱水机中注入比重剂和高分子絮凝剂,以便于形成大的絮团,增加泥水的密度差。
离心脱水机利用转鼓高转速和转鼓与螺旋轴之间的转速差来实现固液相分离。离心机的分离因数与转鼓转速的二次方成正比,为了提高固液相分离效果,便需要转鼓有很大的转速,同时转鼓和螺旋轴要有一定的转速差,这点决定了离心脱水机具有耗能高、噪声大、运行成本高等特点。
2.工艺流程比较
炼油厂含油污泥一般由隔油池产生的池底泥和气浮池产生的浮渣混合而成。相比离心脱水机,叠螺脱水机对进口压力的要求较低,正常工况下,经污泥浓缩罐处理后的污泥只要能够自流进入絮凝混合箱即可,而离心脱水机要求有一定的进口压力,因此污泥输送泵在离心脱水机处理污泥的工艺流程中不可缺少,这样就会增加污泥处理成本;相比叠螺脱水机,离心脱水机在处理炼油厂污泥时,需要投加比重剂,以此来增加泥水密度差,从而提高泥水分离效率,这样也会增加污泥处理成本。
3.运行成本比较
二种脱水机在药耗和水耗方面相差较大;离心脱水机的电耗约是叠螺脱水机的10倍。叠螺脱水机在节约能耗方面具有很大的优势,相比离心脱水机,叠螺脱水机操作、管理、维护简单,污泥处理流程中可以省去污泥输送泵,降低运行成本。
4.优、缺点比较
二种污泥脱水机处理效果基本相同,与离心脱水机相比,叠螺脱水机滤后液SS的浓度略低,表面叠螺脱水机对固体的回收率略高。针对国内炼油厂污水处理场污泥量大增,尤其是浮渣量比例显著增加的现状,采用离心脱水机处理炼油厂污泥,不仅会增加运行成本,而且处理效果难以保证;而采用叠螺脱水机可以在保证处理效果的前提下节约能耗、降低运行成本以及改善工作环境。作为一种新研发的污泥处理设备,叠螺脱水机目前的投资成本略高于离心脱水机。
近几年,我国部分炼油厂在污泥处理中逐步引进叠螺脱水机,经国内某大型炼油厂的实际运行监测,与原有的离心脱水机相比,叠螺脱水机具有噪音小、操作简单、运行稳定、节约能源等优点。它的成功应用,充分证明了其在炼油厂“三泥”处理中有较高的应用价值,可以在保证处理效果的前提下实现节能环保。
三、结论
1.叠螺脱水机和离心脱水机均适用于含油污泥(主要成分是浮渣)、剩余活性污泥的脱水处理,但是前者不适用于较大硬度颗粒,尤其是含大量砂石、大的金属类物质的污泥脱水。
2.离心脱水机主要是依靠转鼓高转速产生的离心力使泥水分离,而叠螺脱水机主要是依靠螺杆的挤压来实现污泥脱水,两者工作原理上的差别决定了在污泥处理中叠螺脱水机的运行成本明显低于离心脱水机。
3.叠螺脱水机采用全封闭箱体,箱体上有预留恶臭气体处理接口,可以有效地减轻污泥中恶臭气体对周围工作环境的污染。
4.二种污泥脱水机的处理效果基本相同,与离心脱水机相比,叠螺脱水机滤后液SS的浓度略低,效果稍好。
5.炼油厂含油污泥经脱水处理后,滤后液含油量大,主要成分是乳化油,直接排入污水处理系统可能对整个系统造成冲击,需要谨慎对待。