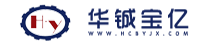
联合站在污水处理过程中,会产生部分的含油污泥和浮渣,此类含油污泥粘度大,站内难以进一步处理,目前主要通过罐车拉运的方式,将污泥储存池内的含油污泥及浮渣,运输至污泥处理,利用传统的排污坑存储方式进行初步处理或固化处理或焚烧处理。传统的处理方法不但成本高昂,还无法完全排除环境污染的隐患,而且在施工中也存在很多的困难,还会带来二次污染。同时,由于处理厂污泥处理较为缓慢,经常无法正常按时拉运浮渣,导致合站污泥池内的浮渣污泥储存过量,而新的污泥又不能及时排出,影响整个污水系统的处理效果。
1 技术原理及简介
浮渣老化油回收处理技术主要包括三部分,初期处理、中期处理和深度处理。初期处理为物理法,包括含油污泥调质、加热、超声辅助破胶、破乳、清洗、机械分离回收原油,可回收90%以上原油,固液分离,污泥含油率可降至2%以下,达到资源化利用目的;中期处理为化学法,固相进入连续混合器,加入新型修复处理剂,通过一系列的物理和化学反应,将其中的残存油、高聚物等有害物质锁定在网链晶格中,形成惰性体不迁移、不溶出,降解、杀灭有害物质、菌类以及臭气等有害气体,催化有机物断链分解,使其转化成类似土壤,进行深度处理;深度处理包括固相生物处理,通过该步处理,污泥含油率可降至3%以下,达到无害化排放目的。
通过现场共同研究讨论,得出了适合于联合站处理含油污泥和浮渣的工艺技术:超声辅助+破胶+破乳+热洗涤+离心分离工艺方法。
工作原理:利用超声波空化、破稳、扰动效应,配合新型油泥破胶剂、清洗剂、抗乳化剂,通过加热搅拌使单一稳定相变为不互溶三相,利用原油凝固点低密度低,通过高速旋转进行分离,原油回收,液体部分循环使用,部分进入深度水处理,固相达到含油污泥资源化综合利用及污染控制技术要求直接铺垫井场。
2 现场应用情况
2.1 设备安装运行
在联合站的建议和配合之下,2016年12月开始进站选址并安装实验所需设备。主要包括两座油泥调质罐、一台燃气油炉和一台三相离心机。
由于含油污泥及浮渣粘度较大,临时焊接一条管线,将站内污泥装车外运管线与实验用调质罐连接,即可利用站内现有污泥泵,将污泥池内的浮渣污泥抽入油泥调质罐内,保证实验项目的连续稳定运行。
2.2 现场应用处理
2016年12月1日,污泥处理实验开始,首先由联合站污水岗员工负责,启动污泥泵将污泥池内浮渣污泥抽入实验用调质罐内储存,利用超声波空化、破稳、扰动效应,配合新型油泥破胶剂、清洗剂、抗乳化剂,通过加热搅拌使单一稳定相变为不互溶三相,利用原油凝固点低、密度低等特点,通过高速旋转进行分离,分别形成油、水、泥三种物质。
通过十天的连续试验,累计处理污泥浮渣260t,处理产生固相物质(泥)20t;回收老化油1.6t,桶装外销;出水水质含机杂小于20mg/1,含油小于2mg/1,直接打回污水处理后端系统。
在联合站配合实验过程中,坚持每天取样三次,进行污泥含油化验。油泥处理前含油率4-8%,油泥处理后含油率<1.63%,达到了固相含油污泥资源化综合利用及污染控制技术要求(含油率<2%),符合资源化利用目的,可直接铺垫井场。
同时还送检2个油样给第三方进行检测,检测结果为含油0.5524%,1.0268%,均<2%。
3 实施效果分析评价
3.1 效果评价
该工艺技术操作简便、占地面积小,可就地进行处理,减少含油污泥及浮渣的拉运费用;工艺连续运行时间稳定,分离效率高,很好回收污泥浮渣里的原油,为企业创造效益;处理后的污水水质机杂小于20mg/1,可直接进行污水处理后端系统,减少脱水及污水处理成本;处理后的固相物质达到含油污泥资源化综合利用及污染控制技术要求(SY/T7301-2016),可直接铺设通井路、铺垫井场;处理费用低,大大降低安全环保风险。
3.2 效益测算
目前,联合站浮渣污泥处理采用装车外运模式,处理成本为1450元/吨,而应用浮渣老化油处理技术后的处理成本仅580元/吨,如果按照年浮渣污泥处理量2024.5t吨计算,年可节约成本176万元。(其中还不包括调剖浮渣污泥量4941.72t,以及回收原油创效)
4 技术创新点
(1)该处理技术的应用有效的避免了建设油泥缓存池、旧油出不去、新油进不来的尴尬局面,作为油田生产环节的一部分,现场处理,不再需要存储和转移处理,降低了成本和运输风险。
(2)具有较好的环境保护效果和经济效益,所出泥土可资源化利用,可用作修路、垫井场、废旧矿山和荒山修复、园林种植等,具有极大的社会效益。
(3)该项目具有低成本特点,资源回收过程中能耗低,与其它油泥处理方法相比,大大降低了处理成本。
5 结论与建议
该技术适用范围广,操作简便,分离效率高,可进行大规模推广应用,具有良好的经济效益及社会效益。