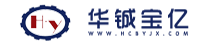
含油污泥是指被丢弃的含油固体和泥状物质,含油污泥主要来源于人类对石油的生产和消费活动。其主要是石油勘探开发业和石油化工行业生产过程中产生的油泥、油砂,具有产生量大、含油量高、重质油组分高、综合利用方式少、处理难度大等特点。含油污泥中除含有大量的残留油类,还含有苯系物、酚类、蒽、芘等有恶臭的有毒物质。含油污泥体积庞大,若不加以处理直接排放,不但占用大量耕地,而且对周围土壤、水体、空气都将造成污染。含油污泥中还含有大量的病原菌,寄生虫,铜、锌、铬、汞等重金属,盐类以及多氯联苯,二英,放射性元素等难降解的有毒有害物质,若不加以有效处理,不仅污染环境,而且造成资源的浪费。因此,含油污泥一直是困扰石油石化行业的一大污染物。
原油开采、油气集输和炼油厂污水处理等过程中都会产生大量的含油污泥。而由于不同作业产生的含油污泥性质不同,还没有一种工艺适用所有油田的含油污泥处理。现今国内外处理含油污泥的方法一般有:焚烧法、生物处理法、热洗涤法、溶剂萃取法、化学破乳法、固液分离法等。但到目前为止,国内油田对含油污泥的处理和利用尚处于试验和研究阶段,尚无可靠的技术、工艺,及运行稳定的处理与利用示范工程。近年来学者针对含油污泥的研究多集中在含油污泥中原油的回收,关于剩余固体含油污泥净化处理方面研究的很少。大部分油田处理含油污泥的方法都 在将含油污泥中的原油进行回收,剩余固体堆积在井场或者挖坑填埋。这种做法不仅不能有效地处理含油污泥,而且对井场及其周围农田的土壤造成了很大污染。目前,含油污泥砂已经被 列为危险废物。
本文针对辽河油田含油污泥的特点,通过对其组分的系统分析研究,参考现今国内处理含油污泥的典型工艺,确定了适合辽河油田含油污泥的较佳处理工艺流程。实验结果表明:该工艺处理该种含油污泥可以有效地回收原油,并且通过混凝处理后,降低了含油污泥中污染物的重金属含量。
1 实验部分
1.1 含油污泥成分及浸出液实验分析
含油污泥样品取自辽河石化炼油厂的含油污泥池。该污泥池收集炼厂各车间排放的含油污泥,经初步处理除油后,剩余部分放置时间达半年以上。该含油污泥老化严重,外观呈深褐色至黑色,具有浓烈的挥发性有机物气味。
1.1.1 含油污泥的水、油、泥含量分析
实验中污泥含水率的测定采用了 标准的水-油混合体系含水率的测定方法;含水率测定后,采用索式提取法测量固体中的含油率;剩余的砂和杂质(含有机物和挥发性物质)经过滤、洗涤、烘干、静置,得到分离出的砂,称重得出泥砂量;总量与以上三者的差值即为其他有机物及挥发性物质的量。
由分析结果看出,由于含油污泥存放时间较长,乳化现象严重。其含水率和含油率均低于新鲜的含油污泥,且固体含量较高,给处理带来一定的难度。
1.1.2 含油污泥浸出液污染物分析
为了对样品含油污泥进行进一步的了解,方便其处理技术的研究,根据GB5086.2-1997,采用水平振荡法,提取含油污泥浸出液,并对其COD、硫、总铬、六价铬、氰化物等指标进行了检测。
由检测结果可以看出,样本含油污泥呈碱性,其COD和油含量都较高。除此之外,总铬、六价铬、氰化物的含量均高于GB5085.3-1996的标准。这说明,由于长期的放置,该含油污泥乳化严重,继续堆积而不采取合理的技术手段进行回收处理,必将对辽河油田周围土壤造成污染。
1.2 工艺确定
由于样品含油污泥放置时间较长,老化干化现象严重,根据其组成特点,确定处理含油污泥工艺流程。
1.3 加水稀释
考虑到含油污泥本身含水率不高,直接加药会出现搅拌不均匀,增加处理药剂量等问题。且在一定条件下向污泥中加水搅拌可以提高油珠与水珠相互接触的机会,有利于油滴更快地浮在水相上层并分离,但增加含水量就会增加能耗和处理剂的消耗。因此,为了更好地均化样品含油污泥,降低处理难度,在处理前要考虑以一定的比例稀释。
取5个100mL烧杯,称取10.0g含油污泥。分别加入清水,保持液固质量比为2:1、3:1、4:1、5:1、6:1。在加热温度均保持40℃情况下,各加入除油剂5mg/L,并搅拌5min。以除油效果为考察对象。
从考察结果可以看出,在处理条件一致的情况下,确定理想的液固质量比为4:1。
1.4 除油
根据化学表面活性剂的剥离和对原油的乳化作用,通过搅拌使含油污泥砂和表面活性剂充分混合,使原油从泥砂表面剥落,并乳化分散到水中,表面活性剂对油污也有一定的溶解作用;然后油相与水相分离,并附在溶液上层,以此实现原油的回收。
在100mL烧杯中,称取10.0g含油污泥,加入40mL水进行稀释,并加热、搅拌均化。聚阳离子有机活性剂对含油污泥除油的处理是行之有效的。添加表面活性剂对含油污泥进行除油处理。根据含油污泥体系的特点,选择几种阳离子表面活性剂进行种类的筛选。通过比较阳离子型聚丙烯酰胺、小阳离子型、复合4800破乳剂的除油效果,筛选出效果较好的为小阳离子型表面活性剂。为了更好地确定该种表面活性剂的实验条件,下面进行正交实验及单因素实验考察。
1.4.1 正交实验
影响表面活性剂处理效果的因素很多,主要包括温度、表面活性剂加量、搅拌时间、pH值等。但pH值的波动会对后面的混凝有所影响,所以不对pH值进行调整。
对温度、小阳离子加量、搅拌时间三因素进行正交实验。从正交实验的结果不难看出,3个因素的级差值分别为10.56、6.64、4.01。其中级差越大说明该因素的变化对处理效果影响越大。得到各因素影响大小顺序为:小阳离子加量>温度>搅拌时间。
在确定了影响因素的顺序后,对各个因素进行单独考察,以确定较佳的实验条件。
1.4.2 小阳离子加量的影响
控制加热温度为50℃,搅拌5min,在6~40mg/L浓度范围内,选择不同的加量,考察小阳离子的添加量对除油效果的影响。
从考察结果中可以观察到:当小阳离子加量小于10mg/L时,随着小阳离子剂量的增大其处理的效果呈上升趋势。而当加量超过10mg/L后,增加小阳离子的量并不带来明显的效果。因此从处理效果和经济角度考虑,确定小阳离子加量为10mg/L。
1.4.3 温度的影响
温度是对表面活性剂处理效果的第二大影响因素。确定小阳离子加量为10mg/L,保持搅拌时间5min,温度控制在30~90℃范围内。从温度对除油效果影响结果可以看出,随着温度的升高,油回收率是增加的,但当温度达到60℃以后,效果呈下降趋势。温度的升高,可以增加表面活性剂的作用效果,也加速了原油从泥砂表面的剥落。但当温度达到60℃以后,温度越高,水、固、油三相就越难分离,使原油回收率降低。故确定加热温度为60℃。
1.4.4 处理时间的影响
确定小阳离子加量为10mg/L,处理温度为60℃后,对搅拌时间进行了考察。
搅拌时间对处理效果影响较小,从图中可以看出,只有小小波动。为了使表面活性剂与含油污泥充分混合,又不会使处理周期过长,选择3min为较佳搅拌时间。此时原油回收率在50%左右。
1.5 混凝
混凝法是向水中投加无机混凝剂进行混凝,消除胶体的稳定因素,再添加有机混凝剂利用微粒之间的吸引力及布朗运动,使已凝聚的微粒不断扩大形成矾花沉淀,以达到去除重金属、有机物和悬浮物的目的。
在经过除油处理后的含油污泥中复配加入无机混凝剂及有机混凝剂。为了使混凝处理后的上清液可继续回用,此工艺以上清液的COD为检测指标。
1.5.1 有机混凝剂的种类及量的确定
出于经济的考虑,选择硫酸铝为无机混凝剂,对有机混凝剂种类首 行筛选。在对含油污泥进行除油处理后,加入200mg/L的硫酸铝,再加入有机混凝剂(4800,PAM,FO4498,FO4228)各10mg/L进行实验。
从实验结果可以明显看出,PAM效果明显优于其他混凝剂。混凝效果的好坏不但体现在上清液的COD上,也体现在实验的现象上。4800及PAM混凝离心静止后水相澄清,但FO4498和FO4420混凝剂离心后,水相显黄色且不澄清。所以,PAM即可以使固液两相很好地分离,又可以保证上清液回用,故选择PAM为有机混凝剂。
首先选择无机混凝剂硫酸铝加量为200mg/L,考察PAM加量。由考察结果可以看到,在PAM加量为5mg/L时,混凝效果较好,水相COD可下降到182mg/L。但当继续投加PAM后,水中COD值又呈上升趋势。这是由于PAM本身是一种高聚合的有机物,投放到水中会增大水体的COD值,因此投加量过大会导致上清液COD升高。因此选定PAM较佳投加量为5mg/L。
1.5.2 无机混凝剂量的确定
确定了PAM的加量后,为了获得更好的处理效果,使硫酸铝与之复配,考察硫酸铝的加量结果。
从考察结果可以看出,硫酸铝加量为100mg/L时,处理效果较优。继续增加硫酸铝的量,处理效果基本无变化。故选择硫酸铝加量为100mg/L。
1.6 处理后含油污泥浸出液污染物分析
在较优条件下对含油污泥样品进行处理,并根据GB5086.2-1997,采用水平振荡法,提取浸出液分析测定。
经过本工艺流程处理后,样品含油污泥浸出液的COD、含油量及污染物含量都大大降低,达到了预期处理效果。
1.7 处理后上清液指标分析
在较优条件下对含油污泥样品进行处理,并提取上清液,对其中的COD、油、硫含量等污染物进行分析测量。
从测量结果可以得出,上清液的COD、油含量不高,且污染物含量及pH值等指标都较低,可作为稀释水重复使用,降低了处理的成本。
2 结论
(1)该处理工艺为辽河油田老化含油污泥提供了合理的处理技术。
(2)通过该工艺处理含油污泥,可使含油污泥中的油、泥、水三相得到分离,并有效地降低含油污泥的污染物含量。
(3)减少了油田含油污泥对环境的污染,部分原油可回收利用,变废为宝。
(4)本工艺化学药剂使用量少、处理效果高,无二次污染。
(5)处理工艺中的稀释水可循环使用,节约成本。
(6)本流程操作简便,可靠性高,有实用价值,具有显著的社会效益。